How Are Playing Cards Made?
There are three main companies who make playing cards: United States Playing Card Company (USPCC) in the USA, Cartamundi in Belgium, and Legends Playing Cards in Asia. While there are others, these three companies combined produce tens of millions of decks of cards every single year. If you’re using a deck that was purchased at a casino, magic shop, or superstore, it’s likely that you’re using a deck from one of these manufacturers. And if you’re using a deck for gambling, magic tricks, or cardistry, it’s pretty much a given!
Andi Gladwin, Vanishing Inc. cofounder at a playing card factory
The Vanishing Inc. team visited the Cartamundi factory in Belgium especially to understand how decks are made. While much of the process is top secret, we are able to reveal some of the key stages to how playing cards are made. The factory we visited is one of the largest playing card factories in the world, employs 100s of people and is larger than a full-sized soccer pitch. Their goal is to print playing cards non-stop, all day, every day.
There are six key steps to making a deck of cards:
Step 1: Designing the Deck
Designing a deck of cards is surprisingly difficult as decks typically have specific design rules, such as the four quarters having a mirrored design. Specialist designers (such as the ones on the Vanishing Inc. team) work in vector designs within very specific remits to ensure that the cards are designed to the exact specifications required by the printers.
While we have designed playing cards for major brands, most of our decks start with a concept and goal. The Dapper Deck, for example, was a deck designed to be a slick everyday carry deck, whereas the Feather Deck was designed to be a deck used for a special occasion.
Once the design has been produced, the designer then inserts the cards into a special template, with each playing card lined up in a grid. This template allows the files to be printed on one card sheet.
The designer has the option to design just the back, or to design the faces too. We often customise the faces, but build on the established styles and history of playing cards.
Step 2: Choosing the Paper Stock
Playing card manufacturers stock are able to print on a few different paper stocks. And while a finished deck of cards feels very smooth and glossy, the paper actually starts as a matte texture and is then varnished once the cards have been printed. While the exact paper stock we use at Vanishing Inc. is a secret, we can tell you that it comes on large rolls and is so heavy that it needs to be carried by a forklift. Each roll will print approximately 10,000 decks of cards.
Typically, the printer glues two of the rolls of paper together through a machine, which helps make the cards thicker (that’s why when magicians split cards, they are able to peel apart two layers and see glue in the middle). The cards are made thicker to ensure that they are opaque in a game of cards and so that they handle better for sleight of hand magicians and cardists.
At this stage of the process, we also must decide on the type of finish. For example, “air cushion" or "linen finish," which dictates exactly how the cards will feel. If you have seen the bumps on a standard deck of Bicycle playing cards, that’s their air cushion finish.
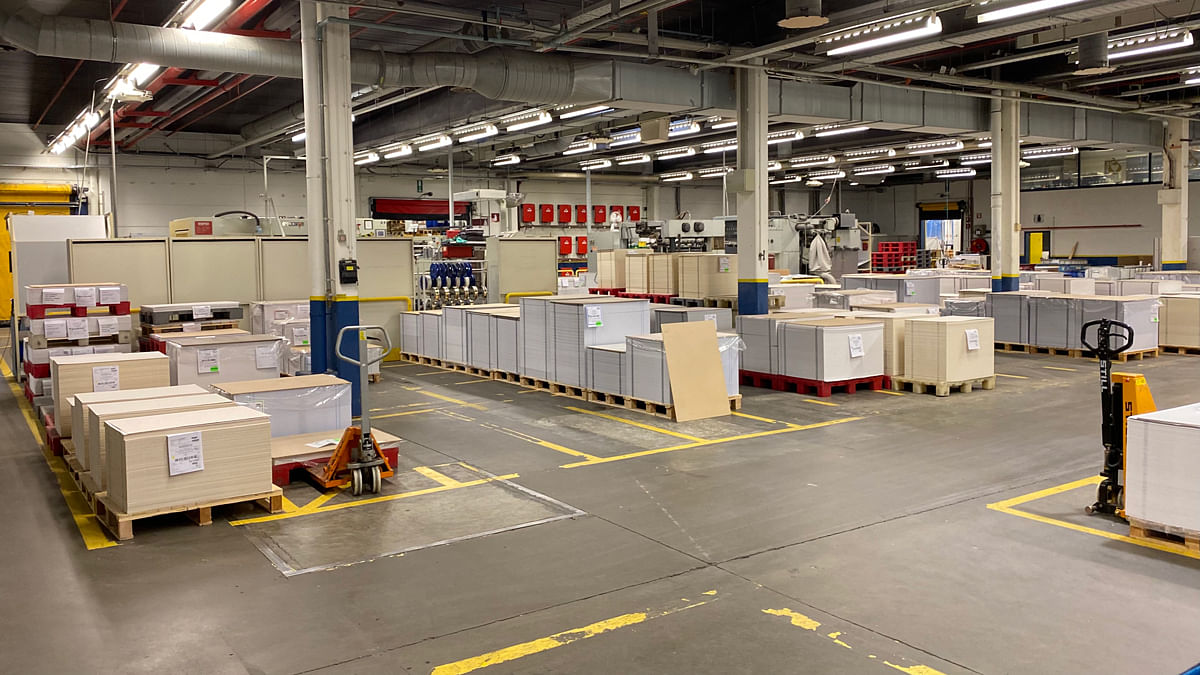
Step 3: Printing the Cards
The playing card manufacturer (such as USPCC or Cartamundi) now prints on that large roll of paper prepared in the previous stage. The printers are about 20 metres long (really!) and the card rolls through them so quickly that looking into the machine is a complete blur. In fact, they print so fast that part of the machine is there to cool the paper down so that it doesn’t burn.
The printers used for playing cards use standard four-ink methodology, just like a laser printer that you might use at home, but on a much larger scale. Instead of ink cartridges, the machines are filled with large buckets of ink! And instead of standard rollers, the design of the deck is laser-etched into specialist printing plates, which tell the machine where to apply the ink.
The machine will also add the finish to the deck at this stage, which is typically a coat of varnish. This finishing process seals the ink, but also makes the deck much nicer to handle.
Once the card is printed, the paper is cut so that there is one deck per sheet. If you have ever seen or purchased a sheet of uncut playing cards, this is where they come from. Playing card manufacturers often remove a few sheets at this stage to save as souvenirs. (And if you’re wondering why they are quite expensive, it’s because any time a human has to interact with a machine of this size, it is difficult and slows the whole process down.)
The printer is able to print and cut about 600 decks per minute. This stage is the quickest part of the process; it really happens in a blur.
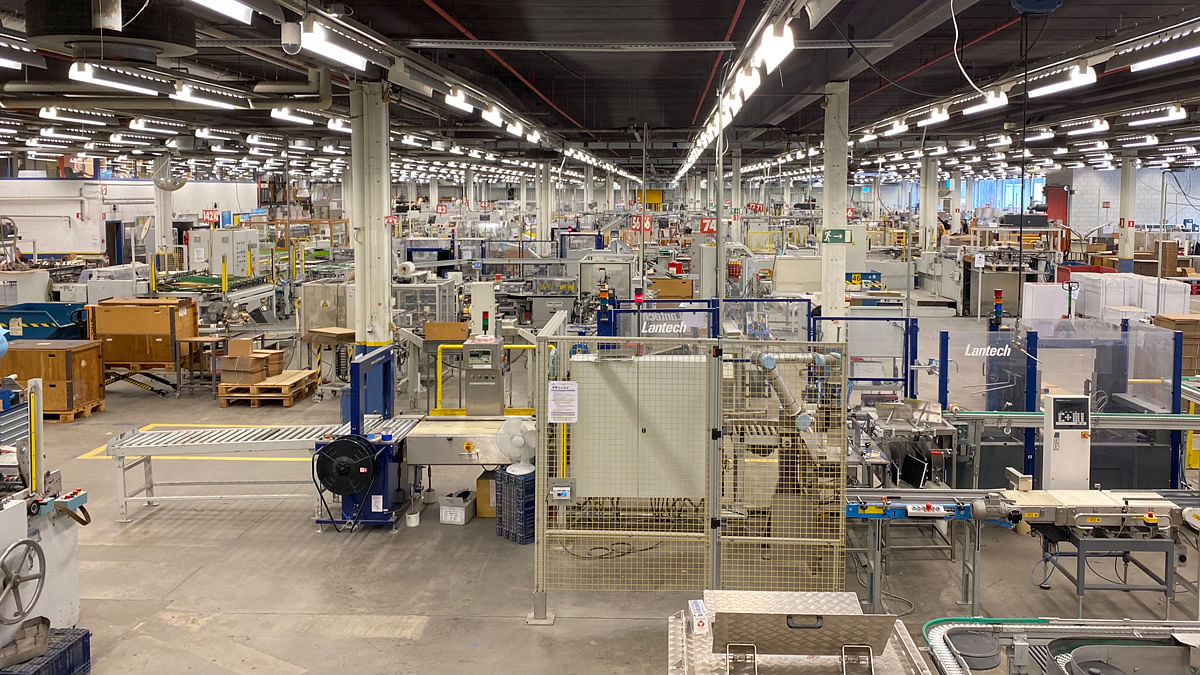
Step 4: Cutting the Cards
Ever heard the phrase "cut the cards?" Well, here we take it to the extreme! The cutting process is different between manufacturers. Typically, the cards are cut out in rows, and then the individual rows are punched out and combined. This is done, automatically, by a machine for each deck. It’s important that the playing card designer organized the file correctly in the previous step because otherwise, at this stage, the cards would be out of order in the deck.
Some playing card manufacturers stamp out the cards in bulk and then run them through a machine to sort them. But as this information is proprietary, they keep the exact process under their hats.
But the important thing to know is that the cards are cut or stamped out on massive guillotines (often laser-guided) using an extremely sharp blade. If the blade were to become dull, the edges of the cards would be soft and bad to handle. For magicians who are looking for the best cards for magic tricks, this would mean that the cards would not faro shuffle well.
Step 5: Feeding into the Box
Whilst the deck is being printed, the card box is also printed and stamped out. Sometimes the boxes are made at a different factory and imported to the printer. A custom-made machine is able to assemble and glue the box, before then sliding the deck into it. It’s an impressive process to watch!
The machine also shrink wraps the deck at this stage. The cards are shrink wrapped to ensure that no moisture gets into them (especially while they ship) and to ensure that when you get your cards, they are in perfect condition. Whether you intend to use your cards for cardistry, card magic, or just to play games, a good condition deck is important!
Step 6: Assembly
The decks are then assembled into boxes (again by machine!) and packaged, once again, to ensure that they are not damaged in transit. Often, a playing card manufacturer like Vanishing Inc. will print 5,000 - 20,000 decks of cards at once and so they are then loaded onto pallets and sent to our warehouse where they are checked for quality, and then eventually sold on our playing cards page.
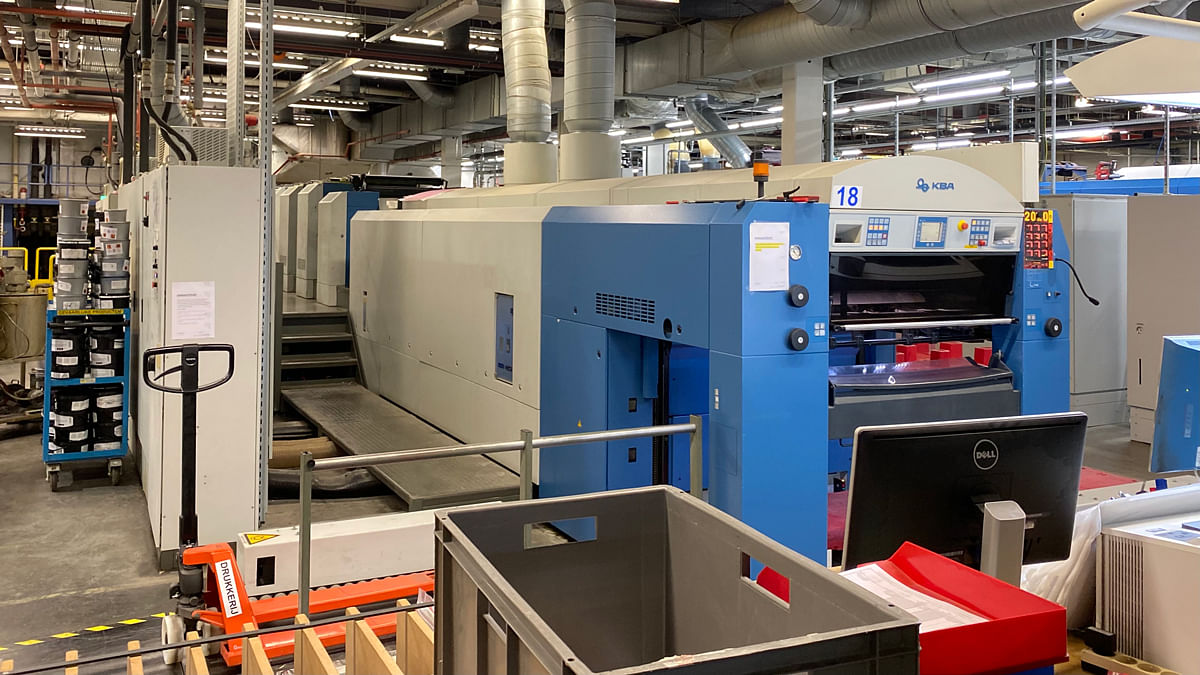
Truthfully, words can’t describe how amazing it is to see a deck of cards go from a file on a computer, to a physical object. The machines handle most of the work, but it takes a whole team of people to run and maintain them.
It doesn't matter if you're going to learn magic from magic-books or from card magic downloads, it doesn't even matter if you're going to be using playing cards for mentalism, virtual magic or magic for children; we all owe thanks to these amazing teams of people. Those coin magic people don't appreciate all this work!
Next time you pick up a deck of cards, spare a moment to the ingenuity and hard work of those who spend their lives perfecting our decks!